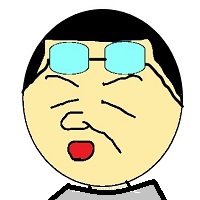
シャフトが摩耗しました。
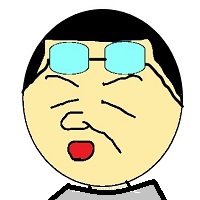
直してもらえますか?
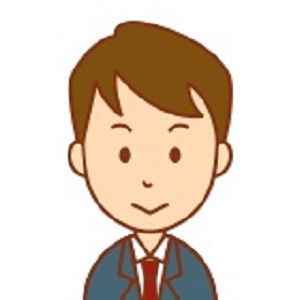
分かりました。
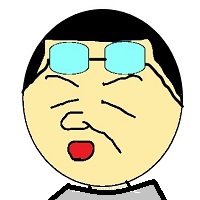
摩耗したシャフトを外すのが
毎回大変なんですが、
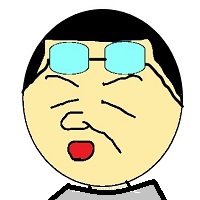
シャフトの寿命を延ばす
いい方法ありませんか?
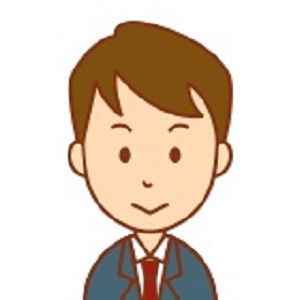
溶射はどうですか?
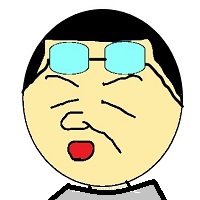
溶射って何ですか?
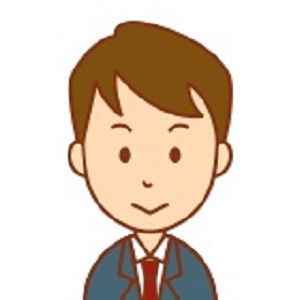
例えば、シャフトの耐摩耗性を
あげたいとき、どうしますか?
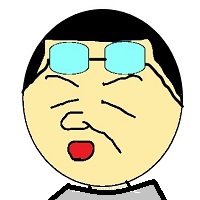
摩耗に強い材質に
変更します。
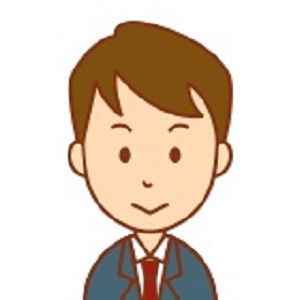
そうしますよね。
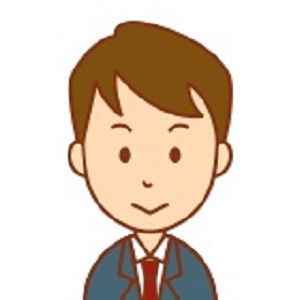
じゃあ、セラミックで
シャフト作りましょう!
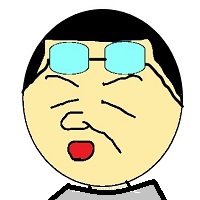
コスト的に無理ですよ・・・。
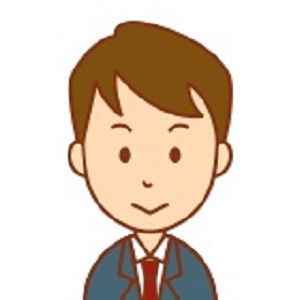
そうなりますよね・・・。
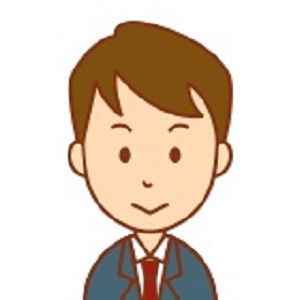
そういう時に使うのが
溶射なんです。
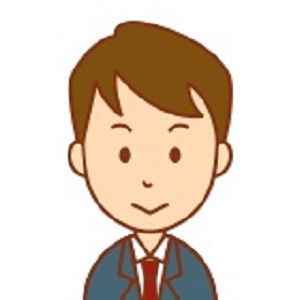
溶射は、一部分だけ基材の表面に
溶射材質を被覆させることで
摩耗に強くさせたり絶縁性を
持たせたりすることが出来ます。
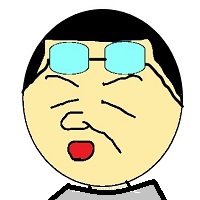
だいたいわかりました。
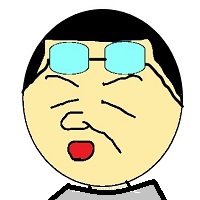
溶射には、どんな種類が
あるんですか?
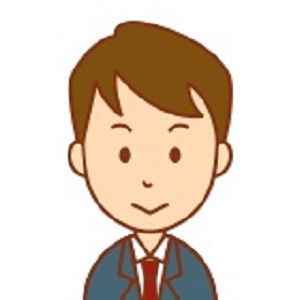
セラミック・超硬・
色んな金属です。
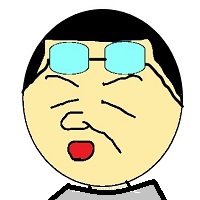
今回、お願いした場合、
材質は何になりますか?
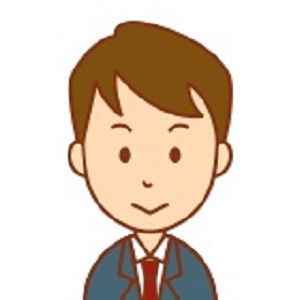
セラミックか超硬
を考えています。
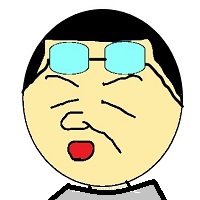
何が違うんですか?
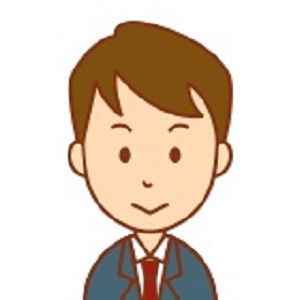
以前は、セラミック溶射が
一般的なイメージでしたが、
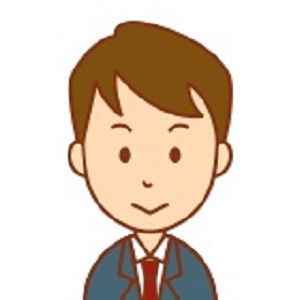
最近は、密着性と耐衝撃性など
の理由で、超硬が増えています。
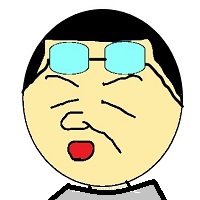
なるほど。
超硬でお願いします。
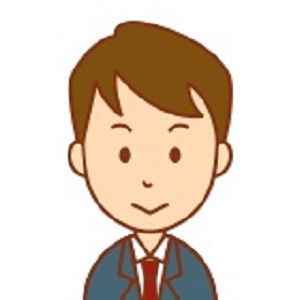
分かりました。
また連絡します。
というやりとりがありました。
今回は、溶射について
簡単にわかりやすく
紹介していきたいと思います。
溶射とは
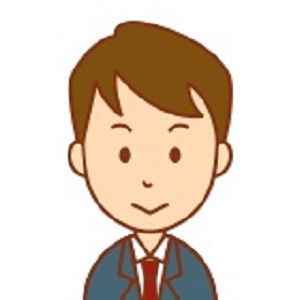
溶射は、
昔メタリコンとも呼ばれ
溶融した金属を
基材に吹き付ける
金属溶射法が、
最初に考えられました。
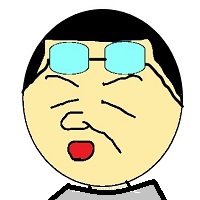
だから、
社名にメタリコンが
ついてる企業さんが
あるんですね。
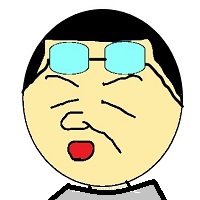
溶射は、どのような
表面処理なんですか?
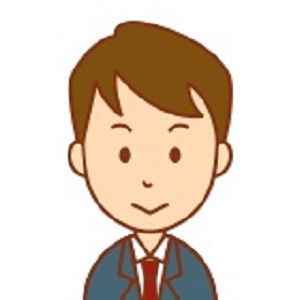
溶射は、
溶融・半溶融の溶射材料を
マッハの速度で基材に衝突させて
被膜を作る表面処理です。
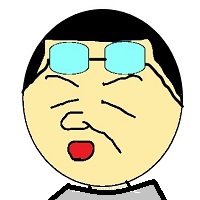
なるほど。
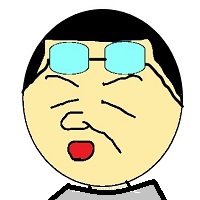
では、溶射する目的を
教えて下さい。
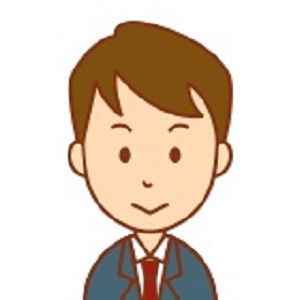
溶射は最初のころは、
メッキ同様、装飾用に
使われていました。
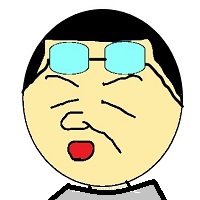
始めは、装飾目的
だったんですね!!
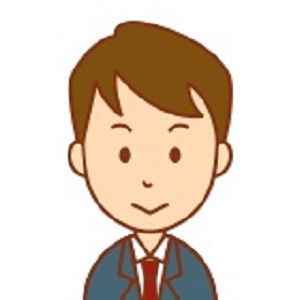
その後、鉄鋼の防錆・防食目的で
使用されるようになってきました。
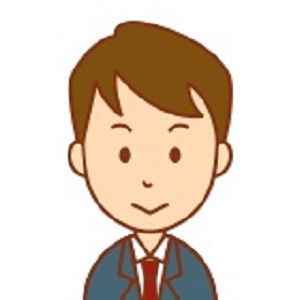
ただ、最近では、
耐摩耗や耐熱性に加え
寸法復元や絶縁・電通性の向上にも
使用されており、機能を向上させる
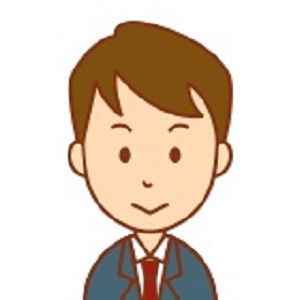
目的で使用されています。
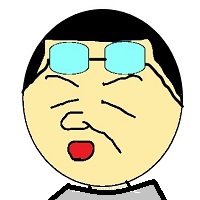
溶射で機能が
向上するんですね。
-
溶射は昔、メタリコンとも
呼ばれていた。 -
溶融した金属を基材に
吹き付ける金属溶射法が、
最初に考えられた。 -
溶射は、溶融・半溶融の
溶射材料をマッハの速度で
基材に衝突させて皮膜を作る
表面処理をいう。 -
最近は、耐摩耗や耐熱性に
加え、寸法復元や絶縁・電通性の
向上など機能を向上させる目的で
使用されている。
溶射が熱で変形しない理由
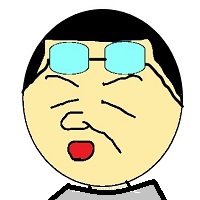
溶射は溶融・半溶融の材料を
基材に衝突させるんですよね?
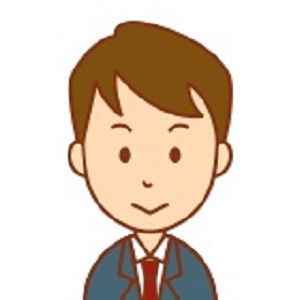
そうです。
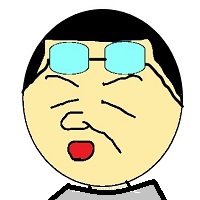
熱で基材が変形しませんか?
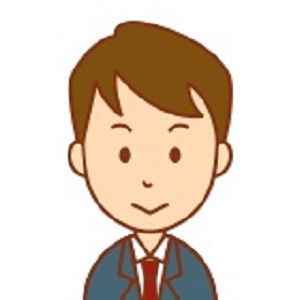
実は、溶射は基材への
熱の影響は少ないんです。
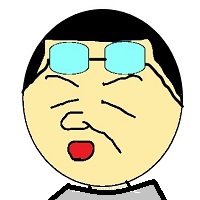
えっ!!何でですか?
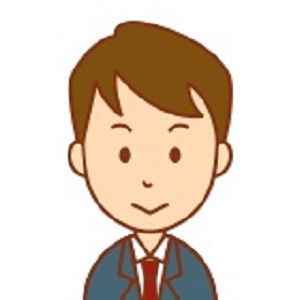
その理由を
簡単に説明します。
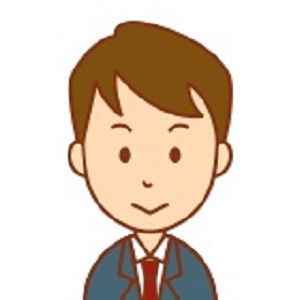
何度も同じ話をしますが、
溶射は高温で溶射材料を
衝突させる表面処理です。
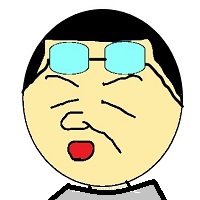
普通に考えたら
溶けた金属が当たるから
基材も熱いでしょ?
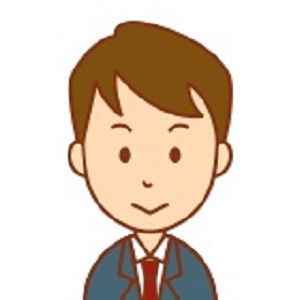
正直、私も最初は
そう思っていました。
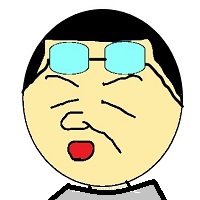
じゃあ、なぜ溶射で基材が
熱で変形しないんですか?
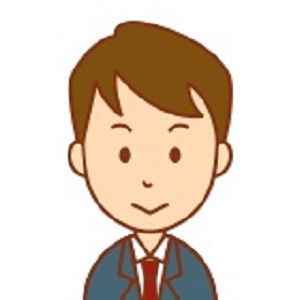
それは、
溶射で吹き付ける、溶射材料の粒子が
0.01~0.1mmと、とても小さいので
溶射粒子が基材に衝突しても
熱があっという間に基材に吸収される
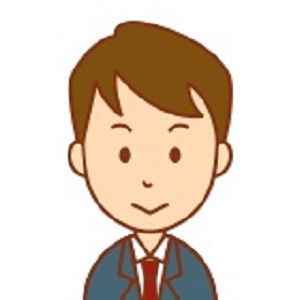
ので基材温度は、
上昇しないんです。
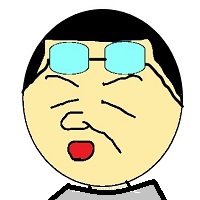
なるほど。
溶射材料の粒子がとても
小さいから影響が出ないんですね。
-
溶射は、基材に対して
熱の影響が少ない。 -
溶射で吹き付ける、溶射材料の
粒子が0.01~0.1mmと、
とても小さい。 -
溶射粒子が小さいので、
基材に衝突しても
熱が基材に吸収されてしまう。
溶射工程
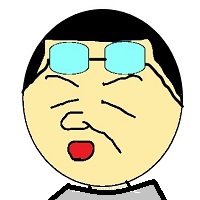
溶射はどのような工程で
作業されるんですか?
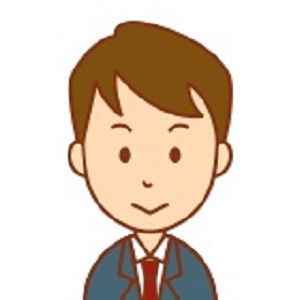
溶射の工程は、
溶射工程 | |
1 | 基材の確認 |
2 | アンダーカット加工 |
3 | 脱脂・洗浄 |
4 | マスキング |
5 | 粗面化処理 |
6 | 溶射 |
7 | 封孔処理 |
8 | 表面仕上げ |
9 | 検査 |
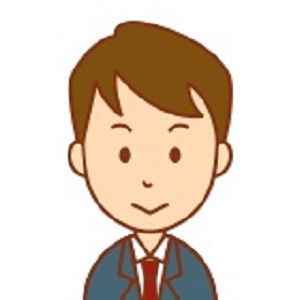
大まかには、
このような工程になっています。
基材の確認
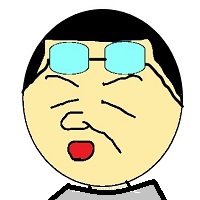
基材の確認って
何をするんですか?
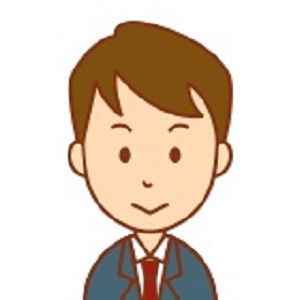
溶射を依頼する前に
溶射が目的の箇所に
出来るかどうかを
確認しておくことが必要です。
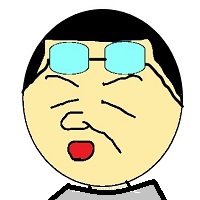
依頼しても溶射できなかったら
意味ないですもんね。
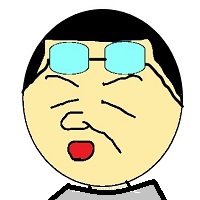
どういう点に
気をつければよいですか?
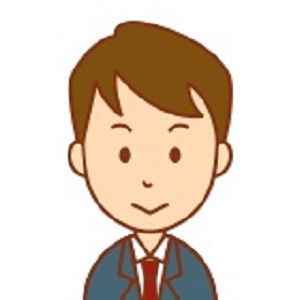
溶射を依頼する前に
確認しておきたいところは、
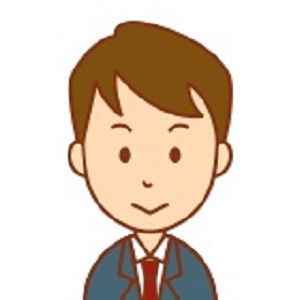
まずは、
『溶射できない死角がないか?』
です。
溶射が届かないような、
内面や狭い箇所など
死角がないかの確認。
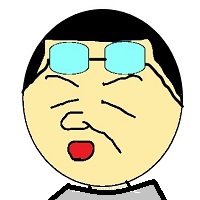
確かに、溶射できない場所には
溶射できないですよね。
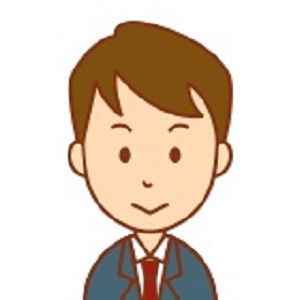
次は、
『板厚は十分か?』
です。
板厚が薄いと、下地処理で行う
ブラスト処理等によって変形や
反りが発生する可能性があります。
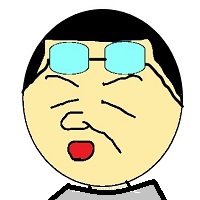
溶射で変形するのではなく
下地処理で変形する場合が
あるんですね。
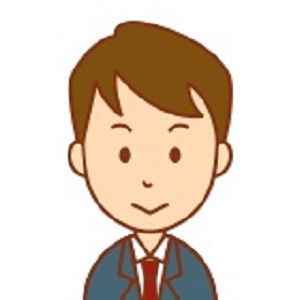
次の確認事項は、
『面取りはされているか?』
です。
端部・角部は基本的に膜厚が
薄くなり割れやすい場所なので、
R1.0やC1.0程度、面取りをしておくと
溶射皮膜が、割れにくくなります。
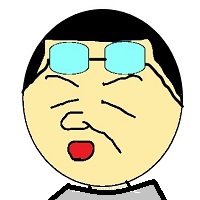
端部や角部がピン角だと
割れやすいんですね。
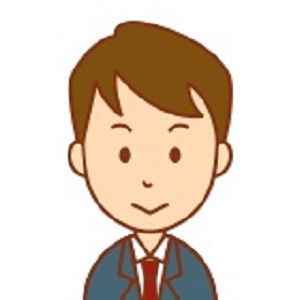
最後に、
『基材の硬さは硬すぎないか?』
です。
基材が硬すぎると、
下地処理が出来なくなる
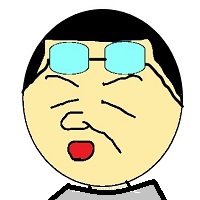
大体どの程度の硬度なら
大丈夫なんですか?
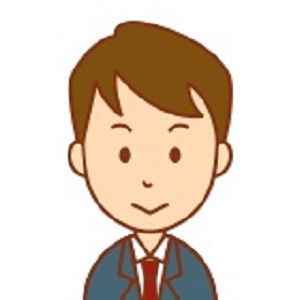
HRC62以下が良いと
言われています。
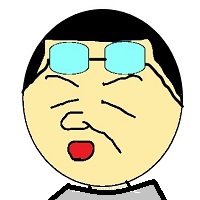
外形寸法を指定したい場合や
膜厚が確保できない場合は
どうすればいいですか?
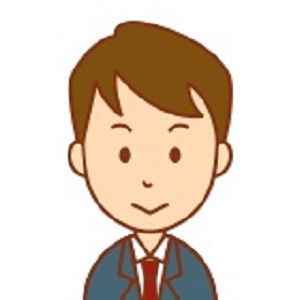
その場合は、溶射する部分を
あらかじめ切削しておきます。
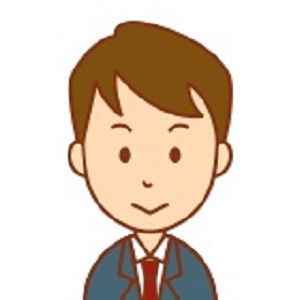
『アンダーカット』
などと呼ばれる
膜厚を確保したり、
密着性をあげる目的で加工するなど
必要に応じて行う工程
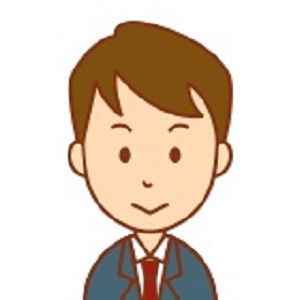
です。
-
溶射を依頼する前に
溶射が出来るかどうかを
確認しておくことが必要。 -
溶射が届かないような、
内面や狭い箇所といった
死角がないか。 -
板厚が薄いと、下地処理で行う
ブラスト処理等によって
変形や反りが発生する
可能性がある。 -
端部・角部はがピン角だと、
溶射が割れやすいので、
面取りしておくと
割れにくくなる。 -
基材が硬すぎると、
下地処理が出来なくなるので
HRC62以下にする。 -
必要に応じて、
膜厚を確保したり、
密着性をあげる目的で
『アンダーカット』
と呼ばれる加工を施す。
前処理工程
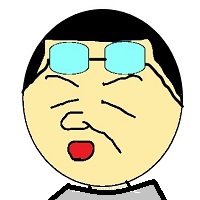
溶射の前に行う
前処理にはどんなものが
ありますか?
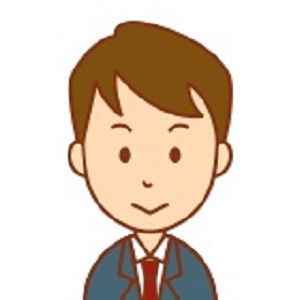
まずは、
『脱脂・洗浄』です。
作業内容は、
- 溶剤や加熱による脱脂
- 高圧水や超音波による洗浄
などがあります。
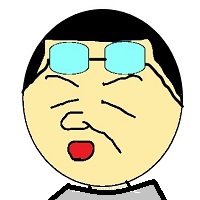
脱脂・洗浄が不十分だと
どうなるんですか?
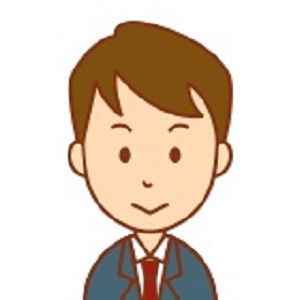
基材表面に、水滴や油脂などが
付着した上から溶射すると
簡単に剥離したりして
使用できない可能性があります。
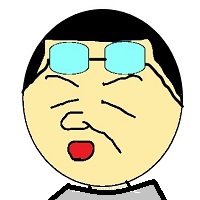
なるほど、それは
十分に、脱脂・洗浄を
行う必要がありますね。
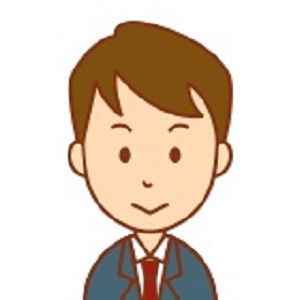
続いては『マスキング』です。
ネジ部や穴部など溶射や
ブラスト処理が必要ではない場所を
マスクして隠すことを
『マスキング』と言います。
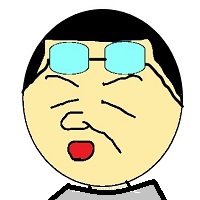
どのようにマスキング
するですか?
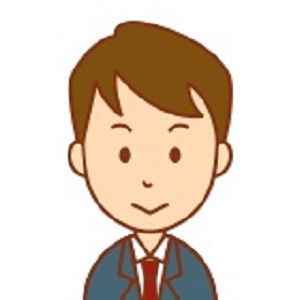
ガラスクロステープや
アルミテープなどの市販品や
マスキング治具や
金属マスクといった製作品を
必要に応じて使用します。
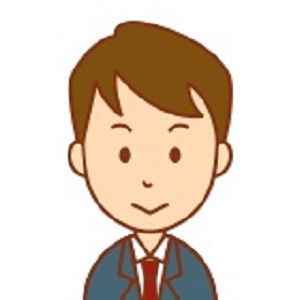
マスキング処理は、かなりの
工数が必要なのでコストアップ
になる場合があります。
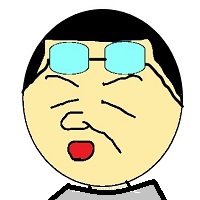
だから、マスキングを依頼すると
コストアップするんですね。
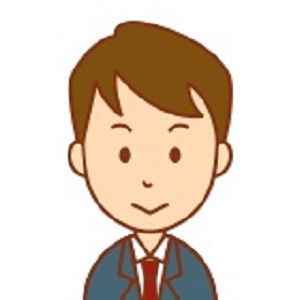
次は、『粗面化処理』です。
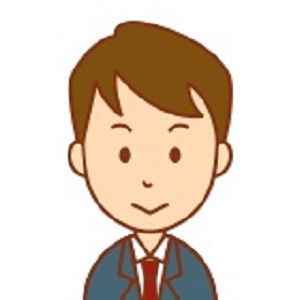
粗面化処理とは、
ブラスト処理などで
基材表面を粗面化することで
付着面積を大きくし、
溶射被膜と基材の接着力を
強くする処理を言います。
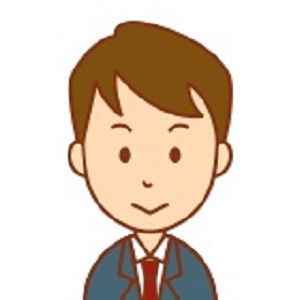
再溶射を行うときの
旧被膜の除去にも
ブラスト処理が使われます。
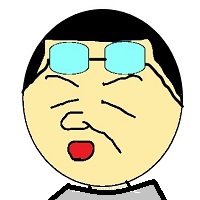
ブラスト処理以外にも
付着面積を増やす方法は
あるんですか?
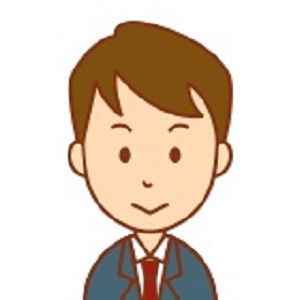
ねじ切りやローレット加工・
溝切り等、機械で加工する
方法もあります。
-
前処理には、脱脂・洗浄・
マスキング・粗面化処理がある。 -
脱脂・洗浄が不十分な状態で
溶射すると剥離したり
使用できない場合がある。 -
マスキングとは、
ネジ部や穴部など
溶射やブラスト処理が
必要ではない場所を
マスクして隠すことを言う。 -
粗面化処理は、
基材表面を粗面化し
付着面積を大きくすることで
溶射被膜と基材の接着力を
強くする処理。 -
再溶射を行うときの
旧被膜の除去にも
ブラスト処理が使われる。
溶射工程
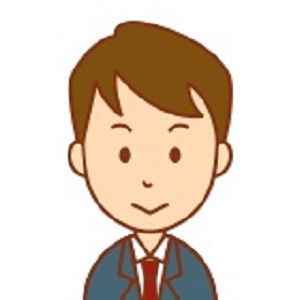
脱脂・洗浄・マスキング・粗面化
などの前処理が完了したら
溶射をかけていきます。
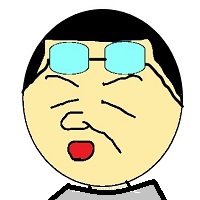
いよいよですね。
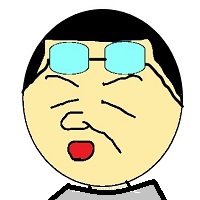
溶射方法に種類は
あるんですか?
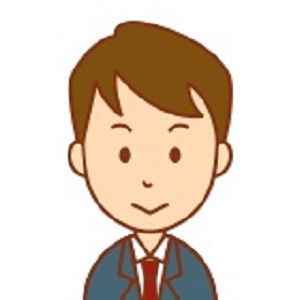
ありますよ。
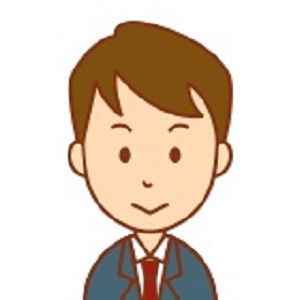
溶射方法は、大きく分けて
- ガス式溶射
- 電気式溶射
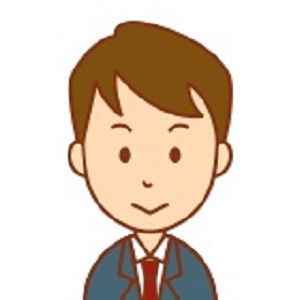
の2種類があります。
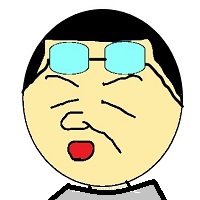
ガス式と電気式ですね。
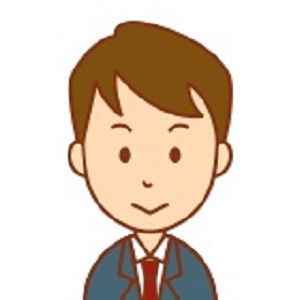
ガス式溶射法は、可燃ガスを
燃焼させて溶射する方法で
- ガスフレーム溶射
- 高速フレーム溶射
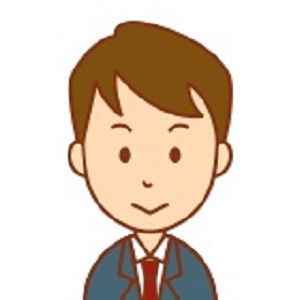
が代表的です。
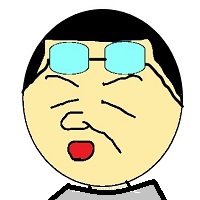
ガス式溶射法の特徴を
教えて下さい。
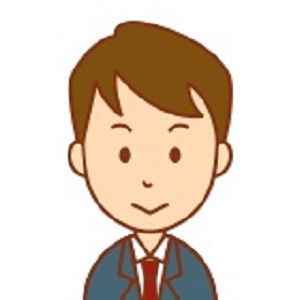
ガス式溶射法は、
粉末・棒状・ワイヤー状すべての
溶射材料が使えます。
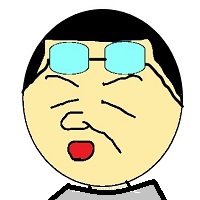
では、電気式溶射法は
どうなんですか?
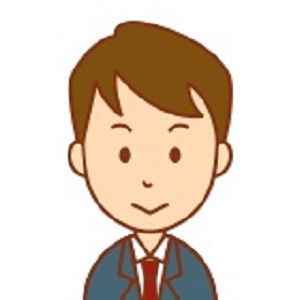
電気式溶射法は、
電気エネルギーを利用して
溶射する方法で
- アーク溶射
- プラズマ溶射
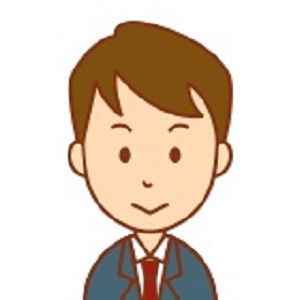
が代表的です。
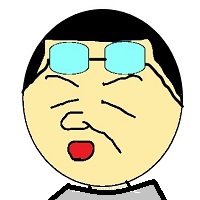
電気式溶射法の特徴を
教えて下さい。
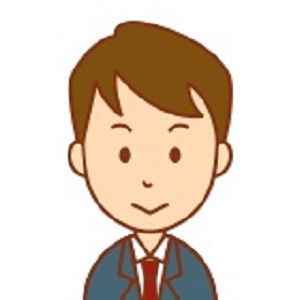
電気式溶射は、
溶射材料が限定され
プラズマ溶射は、粉末のみ
アーク溶射は、ワイヤーのみ
となってしまいます。
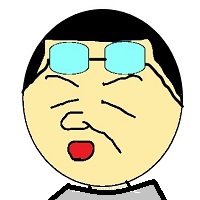
じゃあ、ガス式の方が
便利ですね。
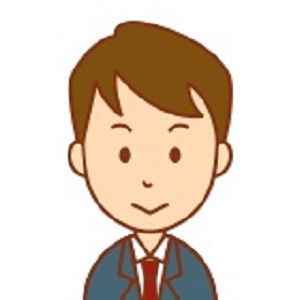
ただ、
電気式溶射はガス式溶射より
ポーラスの少ない溶射皮膜が
出来ます。
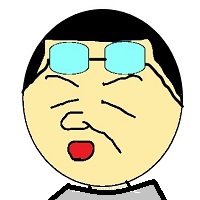
電気式には電気式の
良いところがあるんですね。
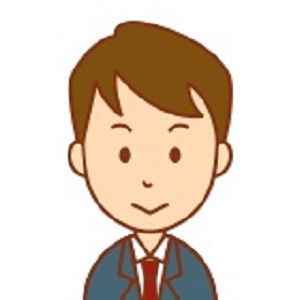
最近では、他の溶射法も登場し
- 爆発溶射
- 高圧・超高速フレーム溶射
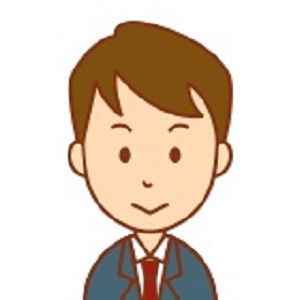
といった、
溶射法も登場しています。
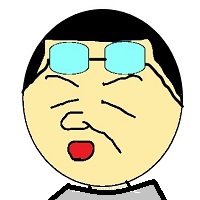
どんな特徴があるんですか?
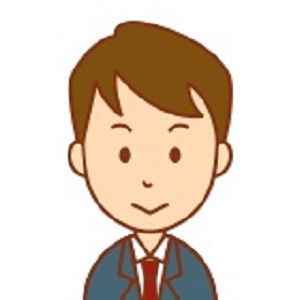
粒子速度が速く、高密度・
高密着・高硬度の特性を持ち、
ポーラスの少ない皮膜を作る
ことが出来る溶射法です。
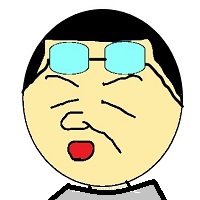
依頼する前に、
溶射メーカーさんに加工方法を
確認したほうがいいですね。
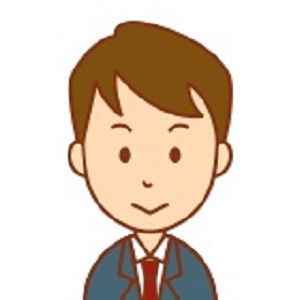
もし、
溶射作業をされるのであれば、
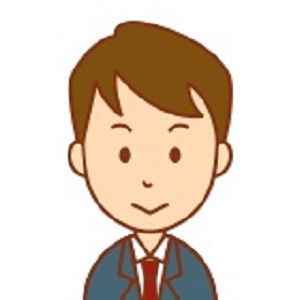
溶射作業中も、
基材を予熱しておくことで
- 水分の除去
- 皮膜の亀裂・剥離防止
- 密着強さの向上
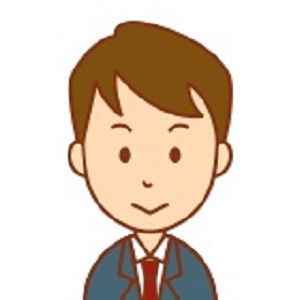
等の効果により健全な皮膜を
得ることが出来ます。
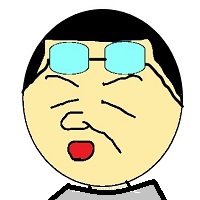
多分、自分で作業を
することはありませんが、
頭に入れておきます。
-
溶射方法には、ガス式溶射と
電気式溶射の2種類がある。 -
ガス式溶射法は、すべての形状の
溶射材料が使用できる。 -
電気式溶射は、溶射方法によって
使用できる溶射材料が
限定される。 -
電気式溶射は、ガス式溶射より
ポーラスの少ない溶射皮膜が
出来る。 -
高圧超高速フレーム溶射・
爆発溶射・といった、
溶射法も登場している。
後処理工程
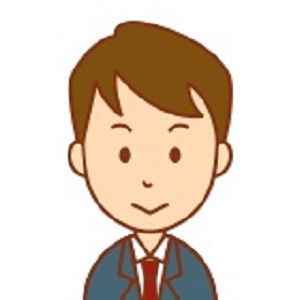
溶射は、粒子の積層によって
構成されているので、多孔質な
仕上がりになってしまいます。
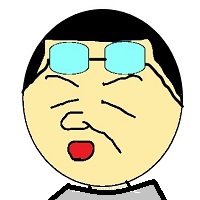
溶射面には、
マイクロクラックがある。
ということですか?
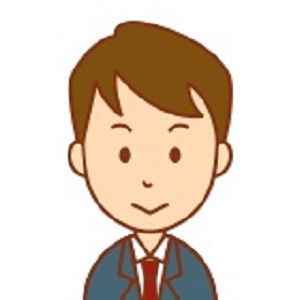
そうです。そのため、
腐食や絶縁・加圧目的の場合
穴をふさぐ、封孔処理が
必要になります。
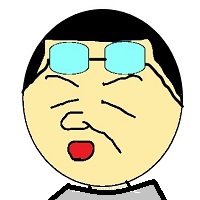
封孔処理はどのような処理を
行うんですか?
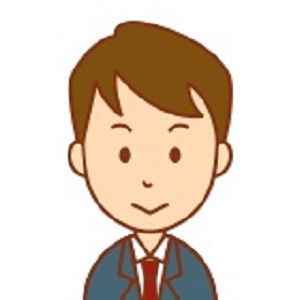
封孔処理は、
溶射の種類や溶射法・
溶射条件によって違う上、
メーカーの機密になります。
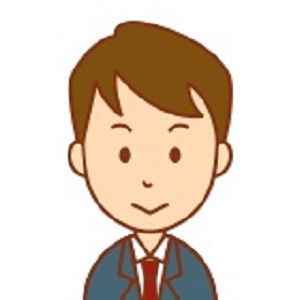
そのため、処理が必要な場合は、
内容を確認して下さい。
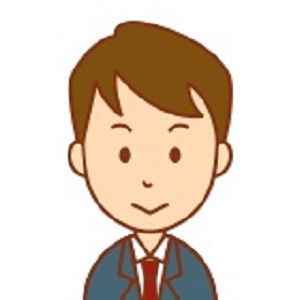
次は、仕上げ処理です。
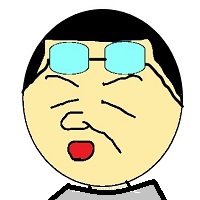
仕上げ処理は、
何をするんですか?
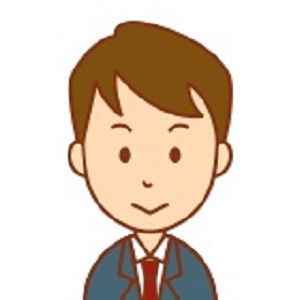
実は、溶射したままの皮膜は、
表面が粗いんです。
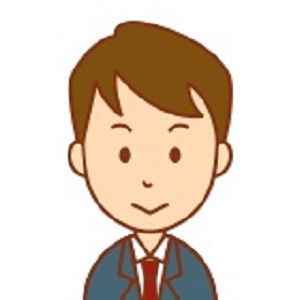
そのため、
寸法精度や面粗さ平滑性など
必要に応じて仕上げ加工を行います。
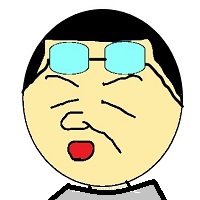
どのような方法が
あるんですか?
切削・研磨・研削といった機械加工や
ラッピングなどの磨き加工を行い
表面を整えます。
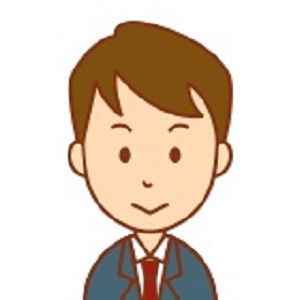
この加工内容によって、
費用が大きく変わる可能性が
あるので注意して下さい。
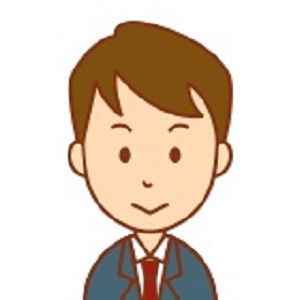
最後に検査して終わりです。
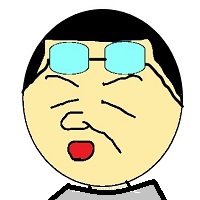
どんな検査をするんですか?
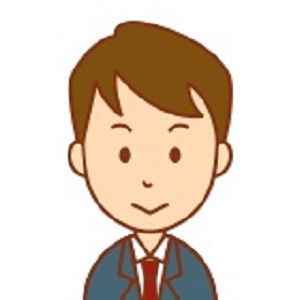
溶射の検査は、
- 外観検査
- ピンホール検査
- 膜厚検査
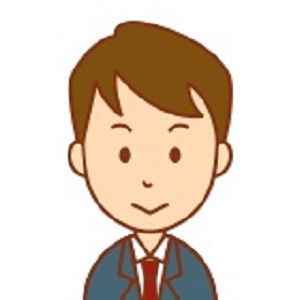
などがあります。
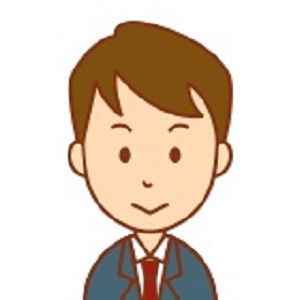
ただ、膜厚測定に関しては、
金属系材料は、通常の
電磁膜厚計では測定が
困難なんです。
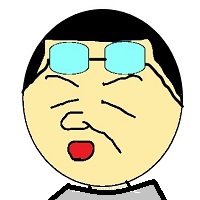
金属系の溶射材料の場合は、
どのような形で膜厚検査を
するかを取り決めておく
必要があるんですね。
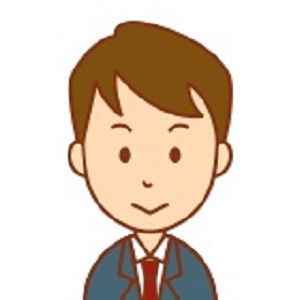
そのほうが、後々、
問題にならないと思います。
-
溶射は、粒子の積層で
構成されるので、多孔質な
仕上がりになる。 -
腐食や絶縁・加圧目的の場合に
穴をふさぐ、封孔処理が必要。 -
溶射したままの被膜は、
表面が粗いので必要に応じて
仕上げ加工をする。 -
溶射の検査は、外観検査・
ピンホール検査膜厚検査・
などがある。 -
膜厚検査に関しては、
金属系材料は、通常の電磁膜厚計
では測定が困難。
溶射材料の特徴
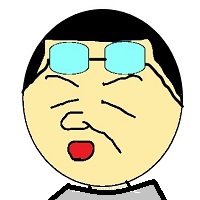
溶射材料には、
どんな種類があるんですか?
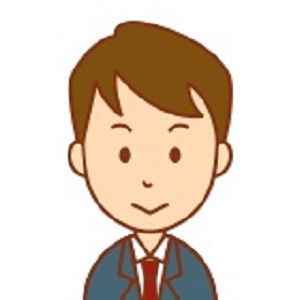
代表的な材料を
紹介していきます。
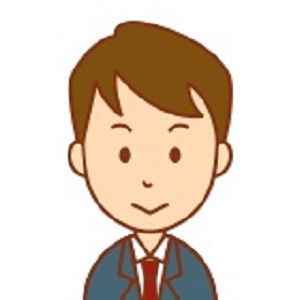
まずは、セラミック溶射材料
から紹介します。
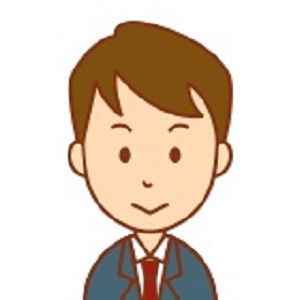
セラミック溶射は、
摩耗に強く、耐熱・遮熱性・
電気絶縁性に優れています。
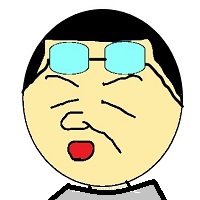
セラミックってすごいんですね。
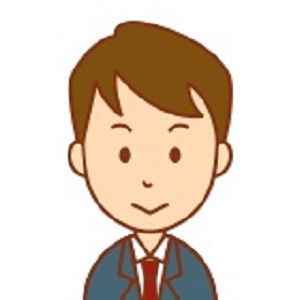
その反面、
靭性が低いので衝撃や
急激な温度変化によって剥離や
亀裂を起こす場合があります。
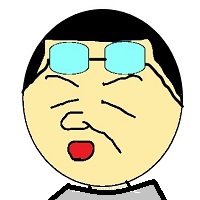
膜厚はどれぐらいに
なるんですか?
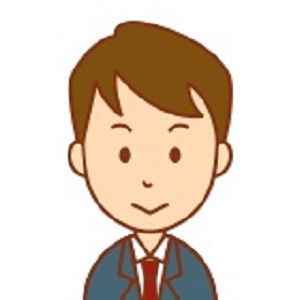
膜厚は、
応力による剥離の危険性から
0.1~0.3mm程度になります。
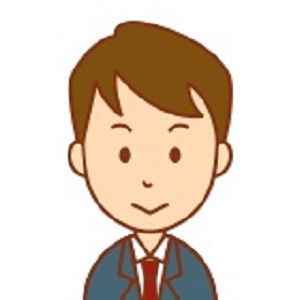
次は、超硬合金溶射材料を
紹介します。
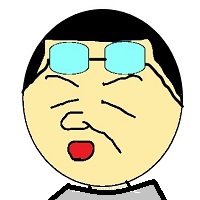
超硬合金は、切削工具とかに
使われてますよね。
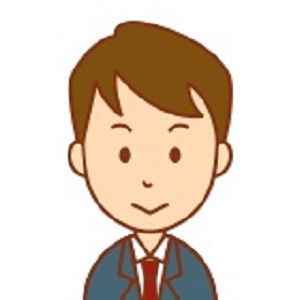
そうです。超硬合金は、
硬さや破壊靭性の特性に優れており、
耐摩耗性や基材との密着性にも
優れた材料
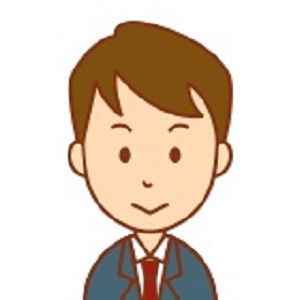
になります。
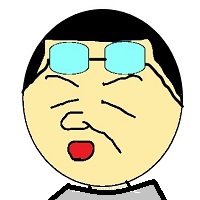
超硬合金の膜厚は
どのくらいですか?
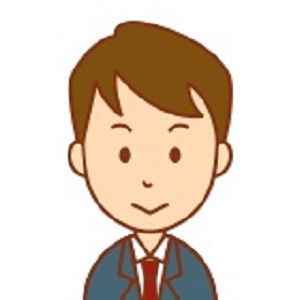
超硬合金の膜厚も、
剥離、亀裂の危険性があるので
0.1~0.3mm程度になります。
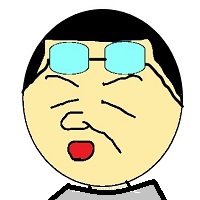
その他の溶射材料は
どんなものがあるんですか?
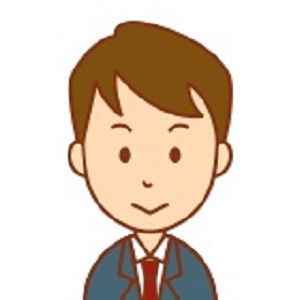
ステンレス・アルミニウム・
銅・ニッケルなど様々な種類の
金属溶射材料があります。
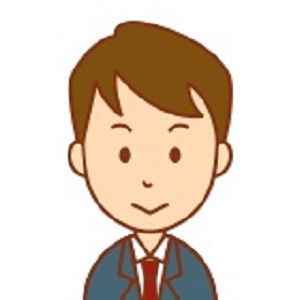
あなたに合う用途に合わせて
選んでください。
-
セラミック溶射は、摩耗に強く、
耐熱・遮熱性・電気絶縁性に
優れた溶射材料。 -
セラミックは、靭性が低いので
衝撃や急激な温度変化によって
剥離や亀裂を起こす場合がある。 -
超硬合金は、硬さや破壊靭性の、
特性に優れており、
耐摩耗性や基材との
密着性にも優れた溶射材料。 -
セラミックと超硬合金の膜厚は、
剥離、亀裂の危険性があるので
0.1~0.3mm程度。 -
金属溶射材料は、
様々な種類があるので用途に
合わせて選ぶ必要がある。
まとめ
溶射は、
機械的特性・電気的特性・熱特性を
基材の一部分だけに
別の特性を持たせることが出来る
優れた表面処理技術です。
基材にセラミックを溶射することで
部品の耐摩耗性や耐熱性を向上させたり
絶縁性を持たせたりすることで
長寿命化や生産性アップにも
つながるかもしれません。
また、
基材を溶かす、肉盛り溶接とも違い
溶射のほうが、同じ寸法復元でも
基材に対するダメージを
少なくできるメリットもあります。
もし、
部品に耐摩耗性や耐熱性・電気特性を
付加させたいと考えているのであれば
一度溶射を検討してみては
いかがでしょうか?
ありがとうございました。